High-quality Sandwich Panel Production Line for Efficient Manufacturing
By:Admin
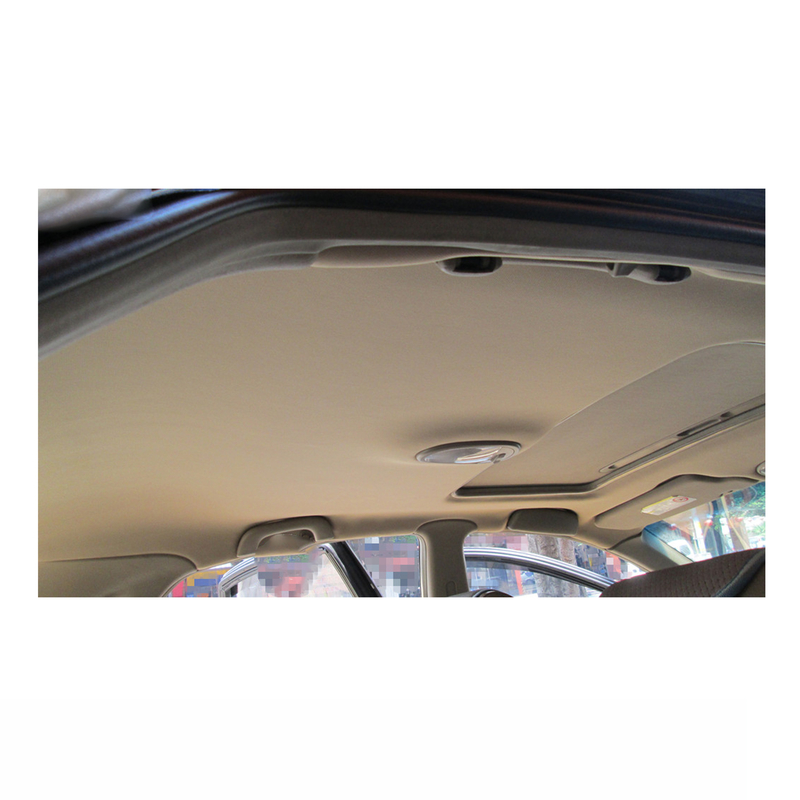
{Company name} is a leading manufacturer of construction materials with a strong emphasis on research and development. With a commitment to innovation and sustainability, the company has established itself as a trusted supplier in the construction industry. The launch of the new sandwich panel production line is a testament to {company name}'s dedication to providing cutting-edge solutions to its customers.
The new production line is equipped with the latest technology and advanced machinery, enabling {company name} to produce a wide range of sandwich panels with precision and consistency. The production line is designed to streamline the manufacturing process, from raw material preparation to the final product assembly. This integrated approach not only reduces production time but also minimizes material waste, contributing to a more sustainable manufacturing process.
One of the key features of the new sandwich panel production line is its flexibility. The line has the capability to produce a variety of panel types, including insulated panels, fire-resistant panels, and acoustic panels, among others. This versatility allows {company name} to cater to the diverse needs of its customers, whether it be for commercial, industrial, or residential construction projects. The production line can also accommodate custom specifications, ensuring that customers receive tailor-made solutions to meet their specific requirements.
In addition to its technical capabilities, the new production line also prioritizes product quality. {Company name} has implemented stringent quality control measures at every stage of the manufacturing process to ensure that the finished panels meet the highest standards. By using advanced testing equipment and adhering to strict quality protocols, {company name} aims to deliver reliable and durable sandwich panels that meet or exceed industry regulations and standards.
Furthermore, the new production line is designed with efficiency in mind. By optimizing the manufacturing process, {company name} can increase production capacity and meet tight delivery schedules without compromising on quality. This efficiency not only benefits {company name}'s bottom line but also provides customers with a competitive edge in their construction projects.
{Company name} is also committed to sustainability and environmental responsibility. The new production line incorporates energy-efficient technologies and responsible manufacturing practices to minimize its carbon footprint. By reducing energy consumption and waste generation, {company name} aims to contribute to a greener and more sustainable construction industry.
As a leader in the construction materials industry, {company name} is continuously striving to innovate and improve its product offerings. The launch of the new sandwich panel production line is a significant milestone that will enhance the company's ability to meet the evolving needs of the construction market. With its advanced technology, flexibility, quality focus, efficiency, and sustainability initiatives, {company name} is poised to uphold its reputation as a trusted partner for construction projects worldwide.
Company News & Blog
Possible causes and solutions for a squeak in 2004-2010 BMW E60/E61 5 Series vehicles
article about the innovative new technology.Introducing the Latest in Mobile Boarding Axle Series: Taking Transportation to the Next LevelAs the world continues to evolve and technology keeps advancing, the transportation industry is not left behind. The latest development in the industry is the innovative Mobile Boarding Axle Series, a cutting-edge technology that offers superior performance, durability, and ease of use.The Mobile Boarding Axle Series is specially designed to provide an efficient solution for loading and unloading goods in heavy-duty vehicles like 18-wheelers, delivery trucks, and buses. With the ability to carry and land all types of cargo, this technology makes transportation safer, faster, and more effective than ever before.The new technology makes use of a patented hydraulic system that is responsible for the vertical and horizontal movement of the boarding axle, which can be used on either the front or rear axles of the vehicle. It also features an intuitive control interface that allows for easy maneuverability and precise positioning during loading.One of the key advantages of the Mobile Boarding Axle system is its ability to reduce loading times, thereby increasing the productivity and efficiency of transportation companies. With a loading capacity of up to 10 metric tons, this technology can handle even the heaviest cargo, making loading and unloading faster and more seamless.In addition to its impressive cargo handling capabilities, the Mobile Boarding Axle Series is also designed with durability in mind. The robust construction and high-quality materials used in its manufacturing are engineered to withstand the daily wear and tear of the transportation industry, reducing maintenance cost and ensuring longevity.Another notable feature of this innovative system is its user-friendly interface, which allows for easy installation and operation. The interface is designed to be intuitive and easy to navigate, making it accessible to drivers, maintenance personnel, and other staff members with little or no technical expertise.In terms of safety, the Mobile Boarding Axle Series is equipped with safety sensors that automatically detect any obstructions or anomalies during the loading process. This ensures the safety of personnel and vehicles by preventing accidents that could arise from using traditional loading methods.The Mobile Boarding Axle Series is the latest innovation in the transportation industry, and it promises to revolutionize the way goods are transported across the world. Its efficient and durable design, coupled with its user-friendly interface and safety features, makes it the preferred choice for transportation companies looking to increase their productivity and efficiency.In conclusion, the Mobile Boarding Axle Series is a game-changing technology that has redefined the way goods are transported. It offers superior performance, durability, and ease of use, making it a valuable investment for transportation companies looking to stay ahead in an ever-evolving industry. With its innovative design, the Mobile Boarding Axle Series is set to transform the transportation industry and take it to the next level.
Mobile Drum Dumper for IBC Loading Streamlines Pharmaceutical Material Handling
Alum-a-Lift, Inc., a leading manufacturer of material handling equipment, has recently introduced a revolutionary product in the market – the 27294 Pharmaceutical Drum Dumper for IBC Loading. This mobile lift is designed to replace several traditional floor-mounted material handling systems and provides a seamless solution for dispensing powder or granular materials into Intermediate Bulk Containers (IBCs) for blending.The pharmaceutical industry is constantly evolving, with new drugs and formulations being developed every day. The process of blending various ingredients to create a final product often requires the use of heavy drums and containers that need to be lifted, transported, and emptied. This process can be time-consuming and labor-intensive, making it a challenge for pharmaceutical companies to streamline their operations effectively.The 27294 Pharmaceutical Drum Dumper for IBC Loading provides a simple and efficient solution for this problem. The mobile lift is designed to lift a floor-bound drum and invert it above an IBC that is on a weigh scale. This allows for the precise dispensing of materials, reducing the risk of errors or contamination. Additionally, the dual lifting stage of this lift allows for transit through standard height doors, making it easier to move from one location to another.One of the key benefits of the 27294 Pharmaceutical Drum Dumper for IBC Loading is its versatility. The lift can be used to handle a variety of different materials, including powders, granules, and liquids. This makes it an ideal solution for pharmaceutical companies that manufacture multiple products or need to handle various ingredients during the blending process.The lift is also designed with safety in mind. The device features multiple safety features, including a manual emergency stop button and an automatic stop sensor that prevents the lift from tipping over. This helps to ensure the safety of the operator and the environment, reducing the risk of accidents or spills.The 27294 Pharmaceutical Drum Dumper for IBC Loading also offers a low-maintenance solution for pharmaceutical companies. The lift is designed to be easy to clean and sanitize, reducing the risk of contamination and ensuring that the products manufactured are of the highest quality. The lift is also designed with durable and long-lasting materials, reducing the need for frequent repairs or replacements.The introduction of this innovative product is a significant development for the pharmaceutical industry. The 27294 Pharmaceutical Drum Dumper for IBC Loading helps to eliminate the need for multiple material handling systems, simplifying the blending process and improving operational efficiency. Furthermore, the device ensures that the blending process is safe, accurate, and consistent, reducing the risk of waste or errors.In conclusion, Alum-a-Lift, Inc has introduced a cutting-edge solution that promises to revolutionize the way pharmaceutical companies handle their materials during the blending process. The 27294 Pharmaceutical Drum Dumper for IBC Loading offers a versatile, safe, and low-maintenance solution for dispensing powder or granular materials into Intermediate Bulk Containers (IBCs) for blending. This device is expected to have a significant impact on the pharmaceutical industry, helping companies streamline their operations, reduce errors, and increase efficiency.
Premium Contour Memory Foam Pillow for Comfortable Sleep
In recent years, there has been a growing trend in the bedding industry towards more comfortable and supportive pillows. One of the most popular options on the market today is the Contour Memory Foam Pillow, which has been gaining praise for its innovative design and ability to provide a better night's sleep.The Contour Memory Foam Pillow is made with a unique blend of materials that are designed to provide the ideal balance of support and comfort. The pillow features a contoured shape that is specially designed to cradle the neck and head, providing targeted support for optimal spinal alignment. This can help alleviate neck and shoulder pain, reduce tossing and turning, and promote a deeper and more restful sleep.The pillow is also made with memory foam, a material that is known for its ability to mold to the shape of the body, providing personalized support for each individual user. This can help to reduce pressure points and improve circulation, leading to a more comfortable and restorative sleep experience.One of the key features of the Contour Memory Foam Pillow is its cooling technology. The pillow is equipped with a special cooling gel layer that helps to regulate temperature and wick away excess heat, providing a more comfortable sleeping environment. Additionally, the pillow is hypoallergenic and dust mite resistant, making it a great option for those with allergies or sensitivities.In addition to its innovative design and advanced features, the Contour Memory Foam Pillow is backed by a company with a strong reputation for quality and customer satisfaction. With a commitment to producing high-quality bedding products that prioritize both comfort and support, the company has quickly become a trusted name in the industry.The company behind the Contour Memory Foam Pillow has a long history of innovation and excellence. With a team of experts in sleep science and product design, the company is dedicated to creating pillows that not only meet the needs of their customers but exceed their expectations. By staying ahead of the latest trends in sleep technology and continually refining their products, the company has earned a loyal following of satisfied customers.In addition to their dedication to quality, the company is also committed to sustainability and environmental responsibility. The materials used in the Contour Memory Foam Pillow are carefully selected for their low environmental impact, and the company takes great care to minimize waste and energy consumption throughout the production process.With its combination of advanced features, innovative design, and a commitment to quality and sustainability, the Contour Memory Foam Pillow has quickly become a top choice for those in search of a better night's sleep. Whether you suffer from neck pain, allergies, or simply want to improve the quality of your sleep, this pillow offers a solution that is both effective and environmentally conscious.Overall, the Contour Memory Foam Pillow is a testament to the success that can be achieved through a combination of innovative design, advanced technology, and a commitment to quality and sustainability. As more and more consumers prioritize comfort and support in their bedding choices, it's clear that this pillow is well positioned to remain a top choice in the market for years to come.
High-Quality Pu Sandwich Panel Machine: Your Ultimate Guide
Pu Sandwich Panel Machine: A Breakthrough in Manufacturing TechnologyWith the advancement of technology, the demand for high-quality and efficient manufacturing equipment is on the rise. In response to this demand, a leading industrial equipment manufacturer in the field of construction and fabrication has introduced a breakthrough product in its line of machinery - the Pu Sandwich Panel Machine.This state-of-the-art Pu Sandwich Panel Machine is designed to provide a cost-effective and efficient solution for the production of sandwich panels that are widely used in the construction industry. The machine is equipped with advanced technology and innovative features, making it a game-changer in the manufacturing sector.The Pu Sandwich Panel Machine is capable of producing high-quality sandwich panels with a variety of materials, including polyurethane, mineral wool, and polystyrene. This versatility allows for the production of panels that are suitable for a wide range of applications, from residential and commercial buildings to industrial structures.One of the key features of the Pu Sandwich Panel Machine is its high level of automation, which significantly reduces the need for manual labor and increases production efficiency. This not only saves time and resources but also ensures consistent quality and precision in the panels produced.Additionally, the machine is equipped with an advanced control system that allows for easy operation and monitoring of the manufacturing process. This system enables operators to adjust various parameters, such as panel thickness and density, ensuring the flexibility to meet specific customer requirements.In line with the company's commitment to sustainability and environmental responsibility, the Pu Sandwich Panel Machine is designed to minimize waste and energy consumption. The innovative production process and materials used result in minimal material wastage and reduced energy usage, making it an eco-friendly solution for the manufacturing of sandwich panels.The introduction of the Pu Sandwich Panel Machine reflects the company's dedication to innovation and continuous improvement in its product offerings. With a strong focus on research and development, the company aims to stay ahead of the competition and meet the evolving needs of the market.In addition to its cutting-edge technology, the company's reputation for superior quality and reliable customer service has established it as a trusted and preferred supplier in the industry. The company's commitment to delivering high-performance equipment and comprehensive support services has garnered a loyal customer base and industry recognition.While the Pu Sandwich Panel Machine represents a significant advancement in manufacturing technology, the company continues to explore new opportunities for growth and expansion. By staying ahead of industry trends and customer demands, the company remains well-positioned to maintain its leadership in the market.The introduction of the Pu Sandwich Panel Machine has generated significant interest and excitement within the construction and fabrication industries. Many industry professionals are eager to experience the benefits and advantages offered by this innovative machine, which is poised to revolutionize the production of sandwich panels.In conclusion, the Pu Sandwich Panel Machine represents a milestone in manufacturing technology, offering a cost-effective, efficient, and sustainable solution for the production of high-quality sandwich panels. With its advanced features and capabilities, this machine is set to make a significant impact on the construction industry, further solidifying the company's position as a leader in industrial equipment manufacturing.
Decorative Panel Making Machine for PVC/WPC Production and Extrusion
Jiangsu Acemien Machinery Co., Ltd. is a renowned manufacturer of plastic extrusion machinery and equipment in China, catering to the needs of the plastic industry. The company is known in the market for its vast range of high-quality PVC/WPC Decorative Panel Making/Production Machine/Extrusion Application, which includes the WPC wall panel extrusion line, PVC ceiling making machine, and wood-plastic panel production line. The equipment has diverse uses and an industry wide reputation. The WPC wall panel extrusion line is designed to produce high-quality wood-plastic composite (WPC) wall panels that are strong, durable, and long-lasting. The production line uses a combination of wood chips, plastic, and other renewable materials to make the composite material that is used for the wall panel. The machine is easy to operate and has high efficiency, making it a popular choice among customers.The PVC ceiling making machine is another key product from Jiangsu Acemien Machinery Co., Ltd. This machine is designed to produce high-quality PVC ceilings that are widely used in homes, offices and public places due to their aesthetic appeal and ease of installation. The equipment has a smooth production process that is characterized by high efficiency, low power consumption, and stable performance.The wood-plastic panel production line is another popular product from the company that is used to manufacture panels that have wood's natural look, texture, and strength, combined with the durability of plastic. The panels are popularly used in various applications such as wall panels, decking, fencing, and window and door frames among others. The production line is eco-friendly, produces less waste and reduces the environmental impact.Jiangsu Acemien Machinery Co., Ltd. has been in the industry for several years, and its salient features comprise excellent after-sales services, high-quality products, rigorous quality control, and customization options tailored to client needs. The company has a state-of-the-art production facility that is equipped with the latest technology, innovative designs, and a professional workforce to meet the diverse needs of its customers."The objective of our company is to provide high-quality plastic machinery and equipment that is long-lasting, eco-friendly, and cost-effective. Our products have earned a reputation in the market and are exported to various countries and regions, including Europe, America, Southeast Asia, and the Middle East," says the company spokesperson.Jiangsu Acemien Machinery Co., Ltd. has been awarded several certifications for its exceptional practices and commitment to quality, including ISO9001, CE, and SGS. The company adheres to strict quality guidelines to ensure that each product is of the highest standard and customer satisfaction is guaranteed.In conclusion, Jiangsu Acemien Machinery Co., Ltd. is a company dedicated to providing exceptional PVC/WPC Decorative Panel Making/Production Machine/Extrusion Application, tailored to meet customer needs, with high efficiency and eco-friendliness. The company's products have wide applications in various sectors, making it a leading player in the plastic extrusion industry. With the latest technologies, innovation, and skilled workforce, the company continues to set new standards in the production of plastic machinery while keeping up sustainable practices.
Understanding the Process of Closed Cell Foam Molding
Closed cell foam molding is a specialized manufacturing process that has been revolutionizing various industries with its unique properties and applications. The process involves injecting a gas into a polymer mix to create a foam with closed cells, which results in a material that is lightweight, buoyant, and resistant to water, chemicals, and temperature extremes. This versatile material has found its way into a wide range of products, from insulation and packaging to automotive components and sporting goods. One company that has been at the forefront of closed cell foam molding technology is {}.Established in {}, {} has been a leading innovator in the field of closed cell foam molding for over two decades. The company's state-of-the-art manufacturing facilities and cutting-edge technology have allowed it to produce high-quality foam products that meet the diverse needs of its customers. With a team of experienced engineers and designers, {} is able to provide custom solutions for industries such as aerospace, marine, automotive, and medical.One of the key advantages of closed cell foam molding is its ability to be molded into complex shapes and designs, making it an ideal choice for products that require lightweight and durable components. {} has developed expertise in creating intricate foam parts that offer superior performance and longevity. Whether it's a specialized insulation component for a spacecraft or a cushioning material for a medical device, the company's capabilities in closed cell foam molding have made it a preferred partner for many leading companies.In addition to its manufacturing prowess, {} is also committed to sustainability and environmental responsibility. The company uses eco-friendly materials and processes in its production facilities, minimizing waste and energy consumption. This aligns with the growing global emphasis on sustainable manufacturing practices, making {} a trusted partner for companies looking to reduce their environmental impact through their supply chain.The applications of closed cell foam molding are vast and varied. One of the key sectors that {} serves is the automotive industry, where lightweight and durable materials are essential for improving fuel efficiency and vehicle performance. The company's foam products are used in various automotive components, including insulation, gaskets, and seals, helping to enhance the overall safety and reliability of modern vehicles.Another important area where closed cell foam molding has made a significant impact is in the marine industry. {} has developed specialized foams that are used in boat and marine equipment, providing buoyancy, impact resistance, and insulation for marine vessels and offshore structures. This has enabled the company to establish itself as a trusted supplier for marine applications, contributing to the safety and functionality of various maritime operations.Furthermore, {} has also expanded its presence in the aerospace sector, where the demand for lightweight and high-performance materials is critical for aircraft design and manufacturing. The company's closed cell foam products are used in aircraft interiors, insulation, and structural components, contributing to the overall efficiency and safety of modern aircraft.As a testament to its commitment to excellence and innovation, {} has received various accolades and certifications for its closed cell foam molding capabilities. The company's dedication to quality and customer satisfaction has earned it a strong reputation in the industry, solidifying its position as a preferred partner for companies seeking reliable and high-performance foam solutions.Looking ahead, {} continues to invest in research and development to further enhance its closed cell foam molding technology and expand its product offerings. With a focus on pushing the boundaries of what is possible with foam materials, the company is well-positioned to meet the evolving needs of its customers and drive innovation across a wide range of industries.In conclusion, closed cell foam molding has emerged as a game-changer in the manufacturing world, and {} has been a driving force behind its widespread adoption. With its advanced capabilities, commitment to sustainability, and track record of delivering high-quality products, the company is poised to shape the future of closed cell foam molding and continue to serve as a trusted partner for industries across the globe.
High-quality 180mm Sandwich Panel for Cool Rooms, Cold Rooms, and Freezers – Industrial Refrigeration Equipment
panels, cold room panels, freezer panels, refrigeration equipment, industrial equipment, and components.When it comes to the construction of cool rooms, cold rooms, and freezers, using the right kind of insulation material is crucial to maintaining the temperature inside the room. This is where sandwich panels come into play. Sandwich panels are highly versatile and come in a variety of sizes and shapes, making them the perfect choice for constructing cold storage facilities.One of the most popular types of sandwich panels used in the construction of cold rooms and freezer rooms is the 180mm fast-fit sandwich panel. This type of panel offers excellent insulation properties, making it an ideal choice for keeping the temperature inside the room consistent and preventing any external heat or cold from entering the room.At (brand name removed), we use the most advanced automatic production line to produce plug boards for our 180mm fast-fit sandwich panels. The foaming material used in the panels is of high quality and ensures maximum thermal insulation. Our panels are easy to install, reducing construction time and improving efficiency.Our sandwich panels are made of two metal sheets – one on the top and one at the bottom – with a core material in the middle. The core material is usually made of a non-combustible material such as mineral wool, polystyrene or polyurethane. These materials offer excellent thermal insulation and are resistant to fire, making them a safe choice for use in cold storage facilities.Our 180mm fast-fit sandwich panels are ideal for use in a variety of applications including food processing plants, pharmaceutical warehouses, and distribution centers. They are also suitable for use in industrial settings where temperature control is critical, such as in chemical and petrochemical plants.Our sandwich panels are manufactured to the highest standards and are engineered to provide the best possible insulation performance. They are easy to clean and maintain, making them a cost-effective and reliable solution for your cold room or freezer room insulation needs.In conclusion, if you are looking for a reliable and efficient insulation solution for your cold room or freezer room, our 180mm fast-fit sandwich panels are the perfect choice. With their excellent insulation properties and easy installation, they provide the most effective barrier against energy loss and external temperature fluctuations. Contact us today for more information on our sandwich panel products.
Latest News Reveals Key Insights on Industry Development and Trends
[Assistant]Title: Heavy Duty Mats Revolutionize Workplace Safety With Advanced Materials and DesignSubtitle: Introducing the Next Generation of Industrial Mats Designed to Enhance Workplace Safety and Productivity[Opening paragraph]In a world increasingly driven by technology and innovation, Mats (brand name withheld) has introduced a groundbreaking line of heavy-duty mats, poised to revolutionize workplace safety standards. With an unwavering commitment to improving the lives of workers across industries, Mats' new collection brings together advanced materials and cutting-edge design to create a safer and more productive work environment.[Company Introduction]Mats is an industry-leading expert in workplace safety solutions, encompassing a wide range of industries such as manufacturing, automotive, construction, and logistics. With decades of experience, Mats has consistently been at the forefront of innovation, developing products that not only meet but exceed safety standards. The company's commitment to quality and excellence has earned them a reputation as a trusted supplier of industrial mats globally.[Body]1. Introduction of Advanced MaterialsMats' latest line of heavy-duty mats is built with the use of advanced materials that provide unparalleled strength, durability, and resistance. Incorporating high-density polyurethane, these mats exhibit exceptional load-bearing capabilities, allowing them to withstand heavy machinery and equipment. The advanced materials also offer resistance to chemicals, oils, and other potentially hazardous substances, ensuring a reliable and safe working surface for employees.2. Enhanced Design for Optimal SafetyTaking design to the next level, Mats has developed a unique pattern on the mat surface that maximizes traction and minimizes slips and falls. The pattern, strategically placed across the mat's surface, provides increased grip and stability, even in wet or oily conditions. In addition, the mats feature beveled edges, reducing the risk of tripping or stumbling for workers navigating the area. With these design improvements, Mats is focused on minimizing accidents and injuries within the workplace.3. Flexibility and Versatility in ApplicationRecognizing the diverse nature of workplaces, Mats' heavy-duty mats offer flexibility in their application. Available in various sizes and configurations, these mats can be customized to fit different work areas, from assembly lines to warehouses. The versatility of these mats ensures that employees are provided with a safe working environment, tailored to meet their workspace requirements.4. Easy Installation and MaintenanceMats' heavy-duty mats are designed with convenience in mind. The lightweight yet sturdy construction enables easy installation by simply placing them in the desired location. Additionally, these mats are easy to clean and maintain, saving time and effort for workers responsible for their upkeep. With minimal maintenance requirements, companies can focus on maximizing productivity while ensuring a safe workplace.5. Environmental SustainabilityAs a responsible manufacturer, Mats remains committed to sustainability. The heavy-duty mats are manufactured using recycled materials whenever possible, reducing the environmental footprint. By opting for eco-friendly alternatives, Mats aims to contribute to a greener and more sustainable future.[Conclusion]In an era where workplace safety is of paramount importance, Mats continues to push the boundaries of innovation with its new line of heavy-duty mats. The incorporation of advanced materials, enhanced design features, and flexibility in application, coupled with a strong focus on sustainability, demonstrates Mats' unwavering commitment to workplace safety and the well-being of employees worldwide. With these mats, companies can now provide a reliable, safe working environment where productivity can thrive without compromising on employee welfare.
High-quality 200L Mixer for Efficient Mixing
Introducing the New 200L Mixer: Revolutionizing Industrial MixingIn today's fast-paced industrial world, efficiency and productivity are paramount. That's why we are excited to introduce our latest innovation, the new 200L Mixer. With its state-of-the-art technology and advanced features, this mixer is set to revolutionize industrial mixing processes and take productivity to the next level.Our company, a leading manufacturer of industrial equipment, has always been at the forefront of innovation and technology. With over 20 years of experience in the industry, we have a deep understanding of the needs and challenges faced by our customers. This understanding has driven us to continuously develop and upgrade our products to meet the ever-evolving demands of the market.The new 200L Mixer is a testament to our commitment to excellence and innovation. It is designed to offer unparalleled performance, reliability, and versatility, making it the ideal solution for a wide range of industrial mixing applications. Whether it's mixing, blending, or homogenizing, this mixer can handle it all with ease.One of the key features of the new 200L Mixer is its advanced control system, which allows for precise and accurate mixing. With customizable speed and mixing settings, users have complete control over the mixing process, ensuring consistent and uniform results every time. This level of control is essential for industries where precision and consistency are critical, such as pharmaceuticals, food and beverage, and chemical processing.In addition to its precise control, the new 200L Mixer is also designed for ease of use and maintenance. Its user-friendly interface and ergonomic design make operation simple and intuitive, while its robust construction ensures durability and longevity. This means less downtime for maintenance and repairs, allowing for continuous and uninterrupted production.Furthermore, the new 200L Mixer is equipped with safety features to ensure the well-being of operators and protect the integrity of the product being mixed. From emergency stop buttons to protective enclosure guards, every aspect of the mixer is designed with safety in mind, complying with industry standards and regulations.With a capacity of 200 liters, this mixer is suitable for both small-scale and large-scale production. Its versatility and adaptability make it a valuable asset for businesses looking to maximize their production capabilities without compromising on quality.The launch of the new 200L Mixer marks a significant milestone for our company and underscores our commitment to providing cutting-edge solutions for our customers. We are confident that this mixer will set a new benchmark for industrial mixing equipment and empower businesses to achieve new levels of efficiency and productivity.Our dedication to quality and innovation is reflected in every aspect of the new 200L Mixer, from its design and performance to its user-friendly interface and safety features. We are excited to bring this game-changing equipment to the market and look forward to seeing the positive impact it will have on our customers' operations.In conclusion, the new 200L Mixer is a testament to our company's unwavering dedication to excellence and innovation. It is set to redefine industrial mixing by offering unmatched performance, reliability, and versatility. With its advanced features and user-friendly design, this mixer is poised to become an indispensable tool for businesses across various industries. We are proud to introduce this groundbreaking product and are confident that it will help our customers take their production capabilities to new heights.
Rotary Three Color Injection Molding Machine for Making Slipper Sandals
and Shoe Injection Molding Machine.Have you ever wondered how those colorful and stylish slippers and sandals you love so much are made? Well, wonder no more! The answer is simple - with a Rotary Three Color PVC Shoe Injection Molding Machine.This machine is specifically designed for the production of high-quality slippers and sandals. Its unique features make it an essential tool for manufacturers who are looking to produce slippers and sandals in bulk without compromising on quality. Here are some of its features:1. Efficient rotary systemThe rotary system in this machine makes it possible to produce up to three colors at the same time. It can produce slippers and sandals with intricate designs and patterns that are sure to catch the eye.2. Consistency in quality The shoe injection molding machine ensures that every slipper and sandal produced has the same quality. The machine’s precision and accuracy help to eliminate any errors or inconsistencies that may occur during production.3. Easy to operate This machine is straightforward to operate, making it a favorite among both experienced and inexperienced operators. It comes with an easy-to-use control panel, which makes it easy to adjust the settings to meet specific production targets.4. High production capacityThe shoe injection molding machine has a high production capacity, making it possible to produce a large number of slippers and sandals in a short amount of time. This makes it perfect for manufacturers who are looking to meet large-scale orders.5. Durability The shoe injection molding machine is built to last. Its sturdy frame and high-quality components ensure that it can withstand the rigors of continuous and long-term use.The Slipper Strap Making Machine is another essential tool for manufacturers who want to produce high-quality slippers and sandals. This machine is used to create the straps that hold the slippers and sandals in place. Here are some of its features:1. Customization The Slipper Strap Making Machine is highly customizable, making it possible to produce straps in various sizes and designs. This makes it easier to meet the specific needs of different clients.2. High production capacity This machine has a high production capacity, allowing manufacturers to produce straps in large quantities. This helps to speed up the production process.3. Easy to operate The Slipper Strap Making Machine is straightforward to operate. Its easy-to-use control panel makes it easy to adjust the settings to meet specific production targets.4. Durability The Slipper Strap Making Machine is built to last. Its high-quality components and sturdy frame ensure that it can withstand continuous and long-term use.In conclusion, if you are a manufacturer looking to produce high-quality slippers and sandals, you need both the Rotary Three Color PVC Shoe Injection Molding Machine and Slipper Strap Making Machine. These machines will help you to produce slippers and sandals that are stylish, durable, and of high quality. So invest in these machines today and take your production process to the next level!