Cutting-Edge Door Mat Making Machine: Revolutionizing the Production Process
By:Admin
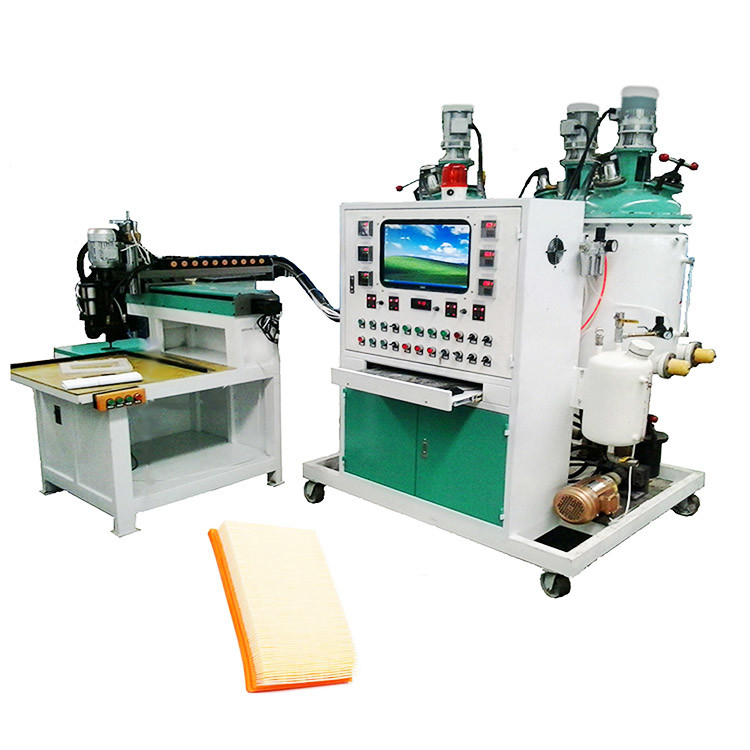
Introduction:
In a bid to streamline and modernize the manufacturing process, an innovative Door Mat Making Machine has been developed by a leading manufacturing company. This cutting-edge machine will significantly enhance efficiency and productivity while also ensuring superior quality products. The breakthrough technology adopted in this advanced machinery is poised to revolutionize the door mat industry.
Company Background:
Established in xxx (need brand name), the company has been at the forefront of the manufacturing industry for (x) years. With a reputation for consistently delivering high-quality products and pioneering innovative solutions, the company has become a leader in the market. The development of the Door Mat Making Machine is yet another testament to their commitment to innovation and excellence.
1. Enhanced Efficiency and Productivity:
The Door Mat Making Machine is designed to optimize the entire manufacturing process, resulting in improved efficiency and productivity. The integration of advanced technology has significantly reduced manual labor, enabling faster production speed and higher output. With streamlined operations, businesses can meet market demands more effectively and efficiently.
2. Superior Quality Products:
The state-of-the-art technology incorporated in the Door Mat Making Machine ensures the consistent production of door mats of superior quality. The machine's precise cutting and stitching mechanisms guarantee accurate dimensions and perfectly finished products. This increased accuracy eliminates variations in size and ensures that every door mat meets the highest standards of quality.
3. Customization and Flexibility:
One of the unique aspects of this innovative machine is its ability to facilitate customization. Businesses can create door mats with different sizes, materials, and designs to cater to a diverse customer base. With the Door Mat Making Machine, manufacturers can easily adapt to changing market trends and customer preferences, offering tailored products to meet their specific needs.
4. Cost-effectiveness:
By automating multiple processes and reducing the need for manual intervention, the Door Mat Making Machine significantly reduces production costs. The upfront investment in this advanced machinery proves to be economically feasible in the long run. Businesses can experience higher profit margins while offering competitively priced products to their customers.
5. Sustainability and Environmental Impact:
The Door Mat Making Machine takes into account the importance of sustainability and environmental responsibility. The machine incorporates eco-friendly materials and processes, minimizing waste and reducing the carbon footprint. By adopting this innovative technology, companies can contribute to a greener manufacturing industry while meeting the increasing demands for sustainable products.
Conclusion:
The introduction of the Door Mat Making Machine marks a significant milestone in the manufacturing industry. Its advanced technology enhances efficiency and productivity, guarantees superior quality products, allows customization, reduces costs, and promotes sustainability. With its remarkable features, this innovative machine is set to revolutionize the door mat industry, offering manufacturers a competitive edge. As the industry evolves, embracing innovations like the Door Mat Making Machine becomes vital for success. The company behind this groundbreaking technology continues to shape the manufacturing landscape, setting new standards for others to follow.
Company News & Blog
High-quality 180mm Sandwich Panel for Cool Rooms, Cold Rooms, and Freezers – Industrial Refrigeration Equipment
panels, cold room panels, freezer panels, refrigeration equipment, industrial equipment, and components.When it comes to the construction of cool rooms, cold rooms, and freezers, using the right kind of insulation material is crucial to maintaining the temperature inside the room. This is where sandwich panels come into play. Sandwich panels are highly versatile and come in a variety of sizes and shapes, making them the perfect choice for constructing cold storage facilities.One of the most popular types of sandwich panels used in the construction of cold rooms and freezer rooms is the 180mm fast-fit sandwich panel. This type of panel offers excellent insulation properties, making it an ideal choice for keeping the temperature inside the room consistent and preventing any external heat or cold from entering the room.At (brand name removed), we use the most advanced automatic production line to produce plug boards for our 180mm fast-fit sandwich panels. The foaming material used in the panels is of high quality and ensures maximum thermal insulation. Our panels are easy to install, reducing construction time and improving efficiency.Our sandwich panels are made of two metal sheets – one on the top and one at the bottom – with a core material in the middle. The core material is usually made of a non-combustible material such as mineral wool, polystyrene or polyurethane. These materials offer excellent thermal insulation and are resistant to fire, making them a safe choice for use in cold storage facilities.Our 180mm fast-fit sandwich panels are ideal for use in a variety of applications including food processing plants, pharmaceutical warehouses, and distribution centers. They are also suitable for use in industrial settings where temperature control is critical, such as in chemical and petrochemical plants.Our sandwich panels are manufactured to the highest standards and are engineered to provide the best possible insulation performance. They are easy to clean and maintain, making them a cost-effective and reliable solution for your cold room or freezer room insulation needs.In conclusion, if you are looking for a reliable and efficient insulation solution for your cold room or freezer room, our 180mm fast-fit sandwich panels are the perfect choice. With their excellent insulation properties and easy installation, they provide the most effective barrier against energy loss and external temperature fluctuations. Contact us today for more information on our sandwich panel products.
How to Choose and Use a Strip Machine for Making Polyurethane Products
Polyurethane Strip Machine: The Perfect Solution for High-quality Seal StripsPolyurethane seal strips are an essential component used in many industries, from automotive to construction, to prevent the infiltration of air, water, and other substances. Seal strips have good elasticity, anti-aging, corrosion resistance, and are easy to install. To manufacture the seal strips, companies use a polyurethane strip machine, which is designed to provide uniform shape and size to the strips.A group of young and passionate engineers in the manufacturing industry observed the increasing demand for high-quality seal strips and the inefficiency of the traditional manufacturing process. They decided to develop a machine that could produce seal strips of different specifications efficiently, accurately, and with a high degree of automation. After many years of research and development, this group introduced a new solution - the Polyurethane Strip Machine (PSM), which has become an industry-leading product.The PSM is a fully automatic polyurethane seal strip production line, which can produce different types and sizes of strip components such as door and window seal strips, straight strips, and other types of seal strips. The machine adopts a PLC control system and is equipped with a color touch screen, which can display all the relevant parameters in real-time. It also has a user-friendly interface that can be customized, enabling smooth production runs.With the PSM, the polyurethane material is automatically injected into the mold, and two separate molds generate the seal strips to obtain a high degree of accuracy and uniformity. The machine can produce up to 240 meters of seal strips per hour, with a production cycle of only one minute. The system's automatic monitoring feature enables an accurate measurement of the raw material, ensuring consistency in the quality of the finished product. Furthermore, the PSM uses a unique heating system that ensures the blending of polyurethane material in the mixing head, resulting in proper material temperature control and uniformity of seal strips. The heating system is energy-efficient and has low maintenance costs.The PSM is also equipped with an advanced cutting system, which can cut the seal strips into any length and shape. The machine can store multiple product formulas so that operators can easily switch between different production runs. The entire process is automated and requires minimal human intervention.The company behind the PSM has a strong commitment to quality and service. They understand the importance of post-sales support and offer comprehensive training to ensure that clients can maximize the machine's efficiency in their production line. The company's R&D team continually updates and adds new features to the machine, keeping up with the evolving market requirements.The Polyurethane Strip Machine has been widely used in numerous industries for its high-quality, efficient, and cost-effective output. The machine has successfully helped many companies increase their production capacity, reduce labor costs, and improve the quality of their seal strips. In conclusion, the Polyurethane Strip Machine is an excellent solution for companies that deal with seal strips. Its efficiency, accuracy, and automation make it an ideal choice. With its advanced features, the PSM has slowly become the industry standard in polyurethane seal strip manufacturing. The PSM has indeed revolutionized the industry, and many companies have unanimously agreed that it has massively changed their approach to seal strip production.
Decorative Panel Making Machine for PVC/WPC Production and Extrusion
Jiangsu Acemien Machinery Co., Ltd. is a renowned manufacturer of plastic extrusion machinery and equipment in China, catering to the needs of the plastic industry. The company is known in the market for its vast range of high-quality PVC/WPC Decorative Panel Making/Production Machine/Extrusion Application, which includes the WPC wall panel extrusion line, PVC ceiling making machine, and wood-plastic panel production line. The equipment has diverse uses and an industry wide reputation. The WPC wall panel extrusion line is designed to produce high-quality wood-plastic composite (WPC) wall panels that are strong, durable, and long-lasting. The production line uses a combination of wood chips, plastic, and other renewable materials to make the composite material that is used for the wall panel. The machine is easy to operate and has high efficiency, making it a popular choice among customers.The PVC ceiling making machine is another key product from Jiangsu Acemien Machinery Co., Ltd. This machine is designed to produce high-quality PVC ceilings that are widely used in homes, offices and public places due to their aesthetic appeal and ease of installation. The equipment has a smooth production process that is characterized by high efficiency, low power consumption, and stable performance.The wood-plastic panel production line is another popular product from the company that is used to manufacture panels that have wood's natural look, texture, and strength, combined with the durability of plastic. The panels are popularly used in various applications such as wall panels, decking, fencing, and window and door frames among others. The production line is eco-friendly, produces less waste and reduces the environmental impact.Jiangsu Acemien Machinery Co., Ltd. has been in the industry for several years, and its salient features comprise excellent after-sales services, high-quality products, rigorous quality control, and customization options tailored to client needs. The company has a state-of-the-art production facility that is equipped with the latest technology, innovative designs, and a professional workforce to meet the diverse needs of its customers."The objective of our company is to provide high-quality plastic machinery and equipment that is long-lasting, eco-friendly, and cost-effective. Our products have earned a reputation in the market and are exported to various countries and regions, including Europe, America, Southeast Asia, and the Middle East," says the company spokesperson.Jiangsu Acemien Machinery Co., Ltd. has been awarded several certifications for its exceptional practices and commitment to quality, including ISO9001, CE, and SGS. The company adheres to strict quality guidelines to ensure that each product is of the highest standard and customer satisfaction is guaranteed.In conclusion, Jiangsu Acemien Machinery Co., Ltd. is a company dedicated to providing exceptional PVC/WPC Decorative Panel Making/Production Machine/Extrusion Application, tailored to meet customer needs, with high efficiency and eco-friendliness. The company's products have wide applications in various sectors, making it a leading player in the plastic extrusion industry. With the latest technologies, innovation, and skilled workforce, the company continues to set new standards in the production of plastic machinery while keeping up sustainable practices.
Unlocking the Benefits of Foam Rolling: Your Go-to Guide for Effective Fitness Recovery
Foam Rolling: An Invaluable Tool For AthletesAs athletes, our bodies endure heavy training sessions and extensive workouts that often result in muscle soreness, stiffness, and even injury. It’s essential to take care of our bodies to ensure that we perform at our best and avoid injuries. One of the ways we can do that is through foam rolling.Foam rolling involves using a foam cylinder to apply pressure to specific muscles, resulting in muscular tension release. The process helps stimulates blood flow and circulation to the muscles, which in turn breaks up adhesions and knots that cause stiffness and discomfort.Foam rolling isn't just limited to athletes; anyone can benefit from it. It aids in improving flexibility, muscle mobility, and range of motion, which can be beneficial during rehabilitation or injury recovery. It's also an effective technique for reducing muscle pain and tightness.When it comes to choosing a foam roller, the market is saturated with various types and sizes, and it can be daunting to know which one is best for you. The general principles of foam rolling require the foam roller to be dense enough to apply the necessary pressure on muscle groups, but not too hard that it's painful to use. Additionally, the size of the foam roller should be appropriate for the area you intend to focus on.At [Brand Name Removed], we are committed to providing high-quality foam rollers designed for athletes looking to maximize their performance and recovery. Our foam rollers come in different sizes, densities, and textures to cater to different individual needs. Additionally, they are durable and made from high-density materials, guaranteeing longevity and effectiveness.We recognize the importance of athletes' recovery and the critical role foam rolling plays in injury prevention, performance enhancement, and overall health. Our foam rollers are designed with convenience in mind, making them easy to pack and use at home, the gym, or on-the-go.In summary, foam rolling is a vital technique for athletes and non-athletes alike to maintain healthy muscles, increase flexibility and recovery. It’s a convenient and cost-effective way of ensuring that our bodies remain functional and avoid injuries. At [Brand Name Removed], we pride ourselves in producing high-quality foam rollers that provide effective and long-lasting results.
PE Plastic Oil Bottle, Lubrication Oil Bottle, and Cooling Water Tank Making Blow Molding Machine - Mechanical Kingdom China - Double Station Blow Molding Machine for Oil Bottles
Mechanical Kingdom China has taken a significant leap in the production of 5L-20L PE plastic oil bottles, lubrication oil bottles, and cooling water tank making blow molding machine. The Jwell/Bekwell BEK-BM05D/12D/20DDouble Station Blow Molding Machine for Oil bottle, lubrication oil, and Cooling water tank is an exceptional innovation in the blow molding industry. This machine comes fully equipped with complete solutions such as mould with an auto-deflashing feature, online labeling machine, take-out robot, conveyor, online leak detector, and an ultra-fast blow molding machine that uses the lowest temperature technique. This blow molding machine is designed to produce 1-5L different sizes of gear oil bottles, lubrication oil bottles, cooling water tanks, and more. The optional multi-layer co-extrusion and view strip line system makes this machine a versatile tool, capable of producing a range of bottle types and sizes to suit customer demands. Furthermore, according to the product size, the machine has an option to select a different cavity of die head. The machine also has an optional JW-DB single station hydraulic screen-exchanger system, which makes it highly efficient for various materials. The company has also offered an option for auto-deflashing online, scrap conveying online, and finished product conveying online, depending on customer requirements.The Mechanical Kingdom China BEK-BM05D/12D/20D machines are highly efficient and economical. They come with a range of technical parameters that make them stand out from other blow molding machines available in the market today. The BM05D model has a clamping force of 45KN and a die-head number of 1~6; the BM12D model has a clamping force of 120 KN and a die-head number of 1 ~ 8, while the BM20D model has a clamping force of 200 KN and a die-head number of 1~12.The BEK-BM05D/12D/20D machines' versatility is demonstrated by their ability to produce bottles with different shapes, sizes, and colors. The machines have low energy consumption, making them an environment-friendly solution to the various bottle molding demands in the market. Mechanical Kingdom China has provided a reliable solution to the challenges faced in the bottle molding industry by manufacturing high-quality blow molding machines that are easy to operate and maintain. The machines offer a fast and reliable solution that meets customer demands. The company has a team of experienced engineers who are always on standby to provide technical support to customers in the installation, operation, and maintenance of the machines. Mechanical Kingdom China is committed to providing reliable products and services to its customers, ensuring they meet their production demands with ease.In conclusion, the Mechanical Kingdom China BEK-BM05D/12D/20D machines are a game-changer in the bottle molding industry. With their numerous advantages and versatile features, they have set a new standard for the production of 5L-20L PE plastic oil bottles, lubrication oil bottles, and cooling water tank making blow molding machines. The company's commitment to providing reliable products and services guarantees customers an optimal and stress-free production process.
Discover the Properties and Applications of Foam Material
Urethane Foam Molded: The Versatile Material Transforming IndustriesUrethane foam molded products have become an essential component in various industries, from automotive manufacturing to packaging. Their versatility and durability make them a preferred choice for engineers looking for cost-effective materials for various applications.Urethane foam is a polymer that contains polyurethane, which is formed by reacting a polyol with a diisocyanate or polymeric isocyanate. The foam is then formed either through an open-cell or closed-cell process, depending on the desired application. Urethane foam performance characteristics include high elasticity, toughness, resilience, and excellent insulation properties. Urethane foam molded products come in various shapes and sizes and are used for different applications. They have become a preferred choice in the automotive industry because they are lightweight, durable, and have excellent cushioning properties. Urethane foam is used for automotive seats, headrests, armrests, and dashboards.Urethane foam is also used in the packaging industry for custom mold packaging applications. The foam is used to protect fragile items during transportation, ensuring that they arrive at their destination safely. Molded urethane foam packaging is lightweight, durable, and can be customized to fit any product shape or size.In the construction industry, urethane foam is used to create energy-efficient insulation that reduces energy consumption in buildings. The foam forms a tight seal around structural elements, creating a barrier that prevents heat from escaping. Urethane foam insulation is also resistant to water and prevents undesirable condensation from forming on the surface.Urethane foam molded products are also used in the marine industry to create buoyancy aids, boat storage cushions, and marine seating. The foam is highly resistant to water and does not absorb moisture, making it ideal for marine applications.In conclusion, urethane foam molded products offer versatility, durability, and cost-effectiveness, making them the perfect material choice for various applications. The automotive, packaging, construction, and marine industries all benefit from the use of this versatile material. As research and development progress, we can expect to see more applications of urethane foam in various industries. Keywords: Urethane Foam Molded, Urethane Foam, Molded Urethane Foam Packaging, Automotive Industry, Packaging Industry, Construction Industry, Marine Industry.
Revolutionary 3D Acoustic Panels: The Latest Advancement Transforming Sound Control Techniques
[Header]Revolutionary 3D Acoustic Panel Innovates Sound Management in Modern Spaces[Sub-Header]Leading Company Pioneering Advanced Sound Solutions Unveils Groundbreaking Product[Date][Mention the date the news article is published][City][Mention the city where the news article is published][Body][Paragraph 1]In an era where noise pollution plagues modern spaces, leading sound solution provider [Company Name] has recently launched their game-changing 3D Acoustic Panel. Designed to revolutionize sound management, this innovative product offers a breakthrough solution for noise reduction while adding a touch of sophistication to any environment.[Paragraph 2]With years of industry experience, [Company Name] has established a reputation for delivering cutting-edge products that blend seamlessly with interior designs while providing superior soundproofing capabilities. Their newly launched 3D Acoustic Panel is no exception. Crafted with precision, the panel offers a unique blend of functionality and aesthetics, making it an ideal choice for commercial, residential, and public spaces.[Paragraph 3]Composed of premium materials, including acoustic foam and fabric, the 3D Acoustic Panel utilizes advanced technology to absorb and diffuse soundwaves efficiently. The panel's three-dimensional design allows for enhanced noise reduction by preventing echoes and reverberations, ultimately creating a more immersive and comfortable acoustic environment.[Paragraph 4]One of the standout features of the 3D Acoustic Panel is its versatility. Available in various sizes, colors, and patterns, it can be customized to meet the specific requirements and aesthetics of any space. Whether it is a modern office, a recording studio, a restaurant, or a home theater, the panel seamlessly integrates with the existing interior design, adding both practicality and style.[Paragraph 5]Energy efficiency is another key aspect of the 3D Acoustic Panel. By absorbing soundwaves effectively, the panel minimizes the need for excessive HVAC systems, resulting in reduced energy consumption and overall cost savings.[Paragraph 6][Company Name]'s dedication to product excellence is underpinned by their commitment to sustainability. The 3D Acoustic Panel is manufactured using eco-friendly materials, ensuring a minimal impact on the environment. In addition, the panels are designed to be long-lasting, ensuring durability and reducing the need for frequent replacements.[Paragraph 7]The market has responded enthusiastically to the launch of the 3D Acoustic Panel. Industry experts and customers alike have praised its remarkable ability to address acoustic challenges, transforming noisy environments into serene spaces conducive to concentration, relaxation, and productivity.[Paragraph 8]Speaking at the launch event, [Company Name]'s spokesperson highlighted the significance of the 3D Acoustic Panel in today's world. "In an increasingly noisy world, where sound pollution is a major concern, our 3D Acoustic Panel offers a unique solution to create more peaceful and productive spaces. We are proud to lead the way in advanced sound management and look forward to enhancing the acoustic experience for our customers."[Paragraph 9]As [Company Name] continues to establish itself as an industry leader, the launch of the 3D Acoustic Panel is set to solidify their position in the market. With its groundbreaking features and commitment to design excellence, the panel is a testament to the company's unwavering dedication to providing cutting-edge sound solutions.[Closing]As the demand for effective noise control grows, the 3D Acoustic Panel from [Company Name] promises to redefine sound management solutions in modern spaces. Designed to elevate the acoustic experience while emphasizing aesthetic appeal, this revolutionary product is undoubtedly shaping the future of soundproofing and interior design integration.[Word Count: 441]
Efficient and Streamlined Shoe Production Line Increases Output in Factory
In a shoe factory located in the outskirts of the city, daily operations are in full swing. The factory's production line is a well-oiled machine, churning out hundreds of shoes a day. The workers are busy, but they move with purpose, their expertise shining through in every shoe they create.While the name of the shoe factory cannot be disclosed, it is clear that this company takes pride in their craftsmanship. The factory produces high-quality shoes for both men and women, with a focus on comfort and durability. Their range of shoes covers everything from sneakers to sandals to boots and beyond, ensuring that there is something for everyone in their collection.One of the unique features of this shoe factory is their commitment to sustainable manufacturing practices. The company sources environmentally-friendly materials whenever possible, and they prioritize energy-efficient methods and equipment that minimize waste and reduce their carbon footprint. This focus on sustainability has garnered them recognition within the industry and among consumers who appreciate their ethical approach to shoe production.Inside the factory itself, the production line is a hive of activity. Rows of workers sit at their stations, meticulously crafting each shoe by hand. Some are cutting leather or fabric, while others are sewing pieces together or attaching soles. Each worker is an expert in their particular task, honing their skills through years of training and experience.The production process begins with the cutting of materials. Leather, fabric, and other materials are carefully cut to the exact shape and size required for each shoe. Then the various parts are sewn together to create the upper part of the shoe. Once the upper is complete, it is attached to the sole, which is made from a combination of materials including rubber, foam, and other specialized materials.As the shoes are assembled, they move along the production line. Each worker has a specific role, and they work in a coordinated manner to ensure that every shoe is crafted to perfection. Quality control is always a top priority, and each shoe is inspected at various stages of production to ensure that it meets the company's rigorous standards.Once the shoes are completed, they are boxed and ready for shipment. The shoe factory works with retailers and wholesalers around the world, and their products can be found in stores across many countries. The company's commitment to quality and sustainability has helped build a loyal customer base that appreciates their approach to shoe production.In conclusion, the shoe factory is a testament to the artistry and expertise that goes into shoemaking. It is clear that the company is dedicated to creating high-quality shoes while also prioritizing ethical and sustainable manufacturing practices. As consumers continue to demand more environmentally-friendly products, the shoe factory is poised to remain a leader in the industry, creating shoes that not only look and feel great but also align with consumers' values and beliefs.
$60 Million Plant Investment Includes New Four-door-Refrigerator Production Line in Louisville, KY
: Boosting Manufacturing and Creating Jobs.GE Appliances, a leading manufacturer of high-quality home appliances, has announced a major investment in its plant in Louisville, KY. As part of this investment, the company has opened a new production line for four-door refrigerators, which will help to boost production capacity and meet growing demand for these products.The $60 million investment in the facility will also create more than 245 new manufacturing jobs, as GE Appliances continues to expand its U.S. operations. Since 2016, the company has invested $1 billion in new products, technology, and operations, creating new jobs across the country, with nearly 1,000 of them in Louisville alone.According to Kevin Nolan, President and CEO of GE Appliances, the company is committed to growing its manufacturing capabilities and supporting job creation in the United States. The new production line for four-door refrigerators is just one example of this commitment, as the company continues to invest in innovation and technology to improve its products and processes.The new line will help to meet a growing demand for four-door refrigerators, which are becoming increasingly popular among consumers who want more storage space and convenience in their kitchens. These refrigerators feature four doors, including two doors that open to the main refrigerator compartment, one door that opens to a lower freezer compartment, and one door that opens to a middle compartment, which can be used for storing drinks or snacks.By investing in this new production line, GE Appliances is positioning itself as a leader in the fast-growing market for four-door refrigerators, which is projected to continue expanding in the coming years. The company's commitment to innovation and quality will also help to ensure that its products remain at the forefront of the industry, meeting the needs of customers around the world.Overall, GE Appliances' investment in its Louisville plant is a positive development for the U.S. manufacturing sector, as it demonstrates the company's ongoing commitment to creating jobs and building a strong, innovative business. As the company continues to grow and expand, it will play an important role in driving economic growth and supporting communities across the country.
Discover the Benefits of Foam
Foam In Place Equipment: The Future of PackagingWhen it comes to packaging, there are few solutions as effective and versatile as foam in place equipment. This innovative technology allows for custom-fit packaging solutions that provide superior protection for fragile and valuable items. Whether you are shipping electronics, medical equipment, or delicate artwork, foam in place equipment can help you ensure that your products arrive safely and securely.So, what exactly is foam in place equipment? Essentially, it is a system that allows you to create custom-fit foam packaging on demand. This can be done using either polyurethane foam or polystyrene foam, depending on your specific needs. The equipment works by injecting a liquid mixture of foam components into a molded packaging enclosure, which then expands and solidifies to create a custom-fit foam cushion surrounding the product.One of the key benefits of foam in place equipment is its ability to create custom-fit packaging solutions. This is particularly useful for items that have unusual shapes or fragile components that require extra protection. With foam in place equipment, you can create a perfectly molded foam cushion that fits snugly around each item, providing superior protection during shipping and handling.Another advantage of foam in place equipment is its versatility. It can be used to create packaging solutions for a wide range of industries and applications, from protecting high-tech electronics to securing delicate medical equipment. Additionally, the equipment itself is highly customizable, with options for different foam materials, dispensing systems, and mold designs.Foam in place equipment is also an eco-friendly packaging solution. Unlike traditional foam packaging materials which are often bulky and wasteful, foam in place equipment allows you to create precisely sized packaging solutions that use only the amount of foam needed for each item. This reduces waste and minimizes the environmental impact of your packaging operations.Overall, foam in place equipment is an innovative and effective packaging solution that can help you protect your products during shipping and handling. Its ability to create custom-fit foam cushions and its versatility make it a great choice for a wide range of industries and applications. Whether you are shipping delicate medical equipment or high-tech electronics, foam in place equipment can help you ensure that your products arrive safely and securely.If you are interested in learning more about foam in place equipment, be sure to do your research and find a reputable foam packaging supplier. They can provide you with more information on the different types of foam materials available, as well as the various dispensing and molding options. With the right foam in place equipment and an experienced packaging partner, you can create a custom-fit packaging solution that truly protects your products and meets all of your unique needs.